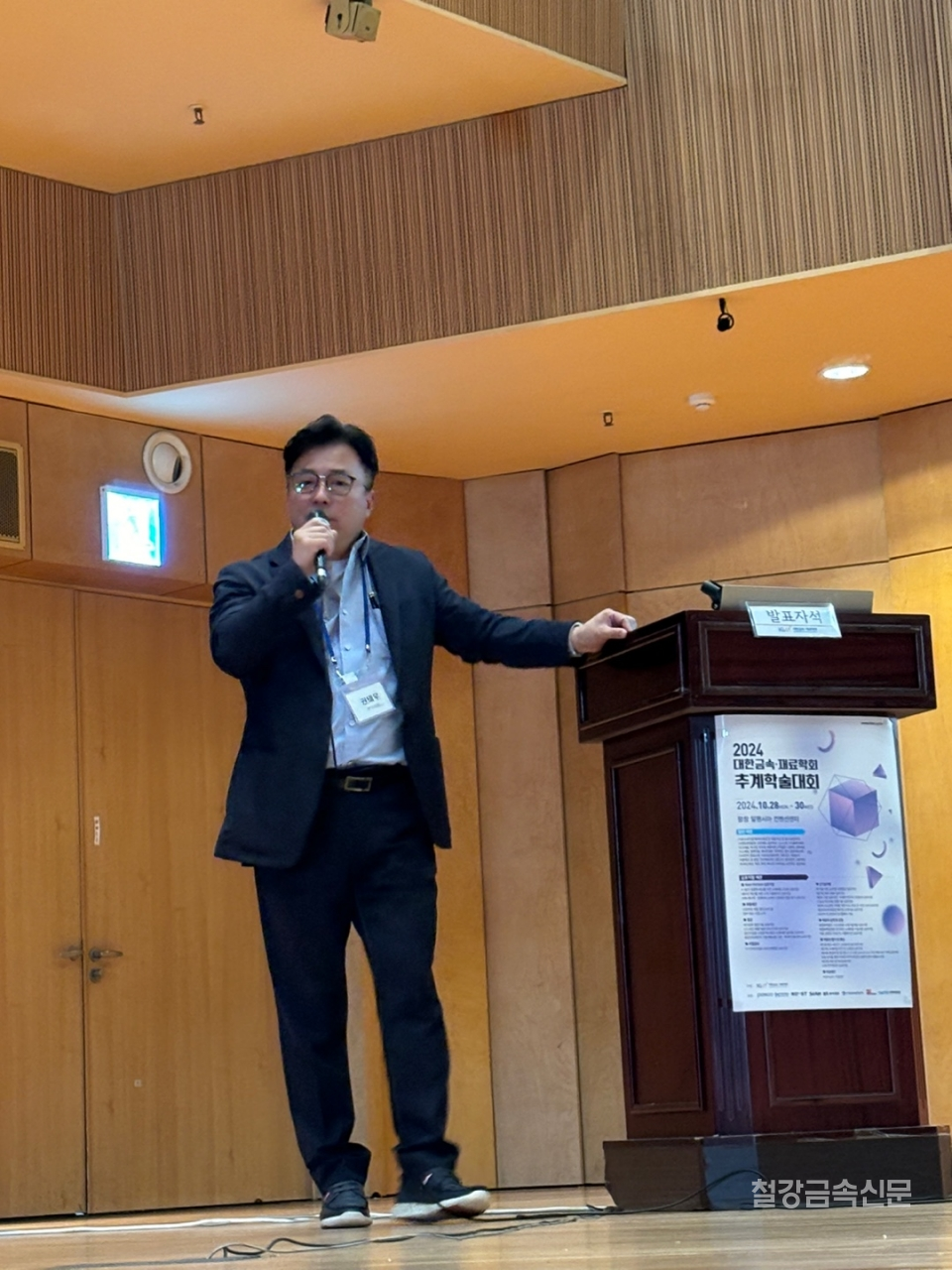
완성차 업계의 전동화 전환에 대응하는 고강도, 경량화 소재 개발이 이뤄져야 한다는 분석이 나왔다.
현대제철 연구개발본부 판재개발실 권태우 상무는 "전 세계 자동차 산업이 전동화 전환 등으로 급격한 변화를 겪고 있다"며 "배터리 증대, 자율주행, 공간 혁신 및 안전 확보 등에 대한 산업적 니즈가 완성차 업계들의 선택이 아닌 규제로 작용하고 있는 만큼 철강 제조사들도 강판 및 부품화 기술 개발을 통해 철강 본원 경쟁력을 확보할 수 있도록 해야한다"고 말했다.
권 상무는 경량화 및 충돌 성능 확보 등 다양한 측면에서 우수한 초고장력강의 적용이 확대될 것으로 내다봤다. 소재별 중량, 비용 및 탄소 배출량을 비교해 봤을 때 자동차 차체와 샤시를 적용하는 경우 초고장력강(강판)과 알루미늄이 가장 현실적이라는 판단에서다. 특히 탄소중립적 관점에서 보면 초고장력강은 1kg 생산 시 약 1.8~2.2kg의 이산화탄소 환산량(CO2e)을 나타냈다. 알루미늄(8~16kg), 마그네슘(20~25kg), CFRP(30~40kg)과는 압도적인 차이다.
권 상무는 냉연 초고장력강과 핫스탬핑강의 개발 방향도 소개했다.
2010년을 기점으로 국내 자동차사의 초고장력강과 핫스탬핑 적용 비율은 크게 증가하고 있는 추세다. 실제로 현대자동차의 NF소나타의 초고장력강 적용 비율은 2009년 21%에서 최근 50% 이상까지 적용비가 확대됐다. 글로벌 주요 완성차 역시 신차 적용 시 시트 크로스 멤버와 센터필러 보강재 등 강도를 기존대비 3~4배 수준 늘리는 등으로 기가파스칼(GPa)급 제품의 개발과 적용을 가속화하고 있다.
아울러 현대제철의 개발 성과도 함께 공유했다.
권 상무는 "현재 당사는 차체 충돌 안정성과 경량화 요구 니즈를 충족할 수 있는 다양한 초고장력강 포트폴리오를 구축하고 있다"며 "냉연 초고장력강 경우 1.5GPa 초고장력강 개발로 응용기술 활용 적용성을 검증한 후 고객사에 양산 공급 중이며, 핫스탬핑강은 1.8GPa 차체 부품 개발과 TMB용 780Mpa(메가파스칼)급 부품을 개발하는 등으로 고객사의 초고강도 소재 니즈 증가에 대응해나가고 있다"고 밝혔다.