강종 개발효과 단기간 입증…소재-완성車 시너지 극대화
AHSS 완성車 적용 높아지며 차량 경량화 지원 '든든'
국내 경제의 밑거름은 제조업이다. 특히 자동차산업은 그동안 꾸준한 발전을 이뤄오며 지난해 국내생산 452만5천대로 세계 5위의 생산대국으로 올라섰다. 중국과 미국, 유럽, 인도 등 해외 생산을 포함하면 800만대 생산을 훌쩍 뛰어넘는다. 조선이나 기계, 가전 등의 제조업이 힘든 시기를 보내고 있는 가운데서도 자동차산업만큼은 발전의 속도를 늦추지 않으면서 한국 경제를 받치는 든든한 한 축이 되고 있다.
자동차에 쓰이는 강판은 첨단 철강기술의 집약체로 철강의 꽃으로 불린다. 가벼우면서도 튼튼해야 해서 철강제품 가운데 공정도 가장 복잡하다. 그러나 한번 공정을 설치하면 대량생산이 가능하다는 장점이 있어 이을 통해 수익성을 극대화할 수 있다. 그만큼 높은 기술을 필요로 하기 때문에 진입장벽도 높아 주요 차강판 생산업체들은 세계적으로 10여개 정도에 불과하다.
현대제철은 모기업인 현대자동차그룹의 철강 전문기업으로 지난 2010년 당진 일관제철소 가동 이후 세계에서도 눈부시게 발전을 거듭하고 있다. 특히 ‘자동차강판 전문제철소’를 지향하며 다양한 신강종 개발 성과를 거두면서 현대ㆍ기아차의 국내외 공장에 고품질의 자동차강판을 안정적으로 공급하고 있다.
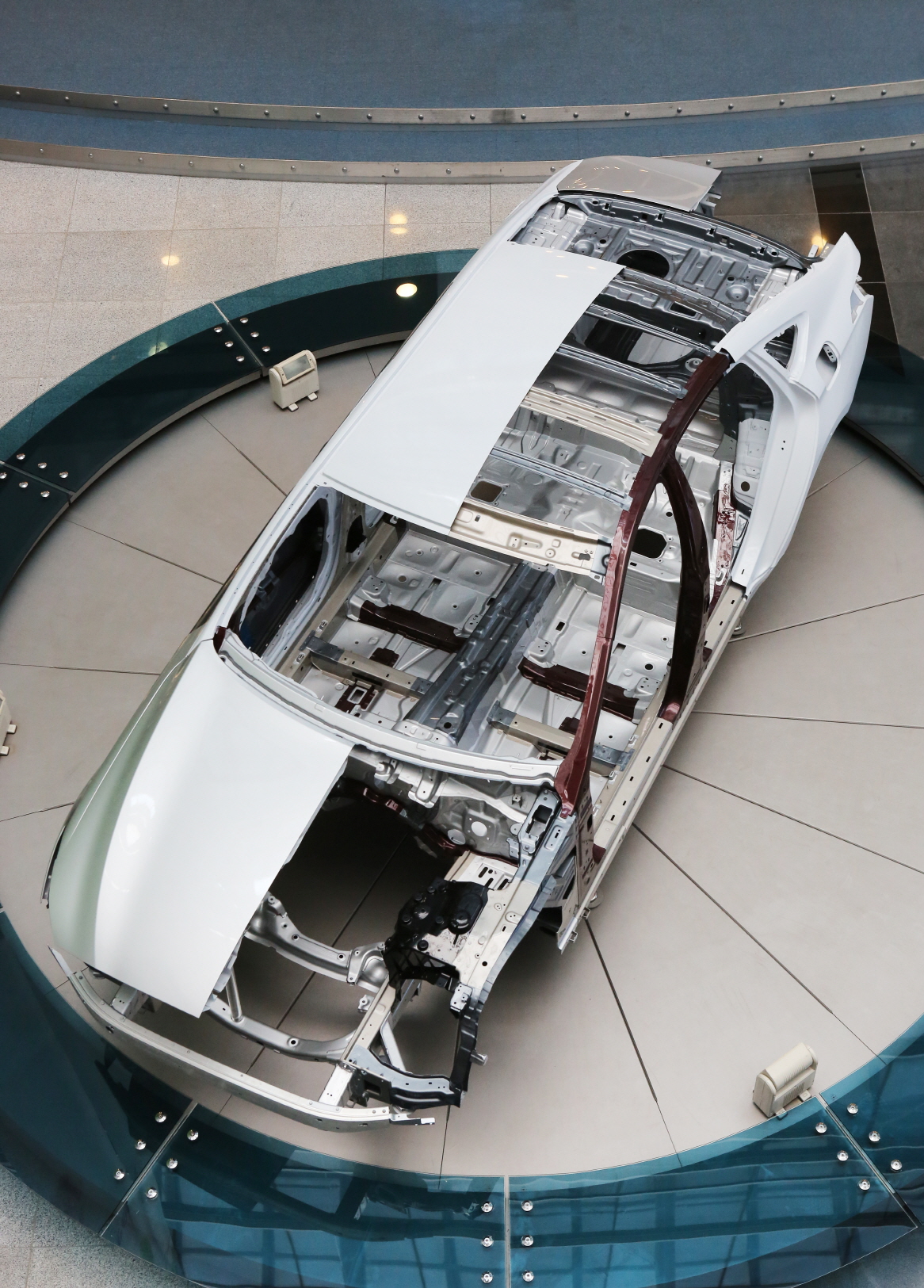
전 세계 고로업체 가운데서는 후발주자이지만 최신 설비의 장점을 최대한 활용하고 현대자동차그룹 내 공동 연구개발을 진행하는 한편 현대하이스코의 합병을 통해 자동차용 강판에 특화된 전문 기업으로 성장하고 있다.
현대제철은 일관제철사업을 시작한 지 단기간 내에 자동차강판 전문 제철소로 자리매김 하면서 냉연사업의 필요성이 부각돼 지난 2014년에 현대하이스코 냉연사업부문만을 인수했다. 이어 불과 1년 만에 현대하이스코의 나머지 사업을 합병하여 고로, 전기로, 열연, 후판, 냉연, 도금강판, 특수강, 철근, 형강, 강관, 경량화, 해외 가공센터 등으로 사업범위를 넓히게 됐다. 이로써 국내에서는 생산품목을 기준으로는 최대의 포트폴리오를 갖춘 종합제철소로 거듭나고 있다.
특히 올해 안정적인 원료 조달 및 열연강판 생산능력에다 기존 현대하이스코의 냉연제품의 제조, 자동차용 강관제품 생산, 해외 가공센터 운용, 경량화사업을 아우르면서 자동차강판 일관 생산체제를 완전히 갖추게 됐다. 여기에 특수강 사업 투자를 통해 자동차용 특수강 소재 생산으로도 발길을 넓히고 있다.
무엇보다 이러한 성장의 밑거름은 세계에서 유례를 찾을 수 없을 정도로 빠른 자동차강판 강종 개발과 양산차 적용에 있다고 할 수 있다. 자동차 생산순위 세계 5위권으로 성장한 현대자동차(기아차 포함)와의 협업체제가 단단히 구축돼 있기 때문이다.
실제로 현대제철은 일관제철소 가동 이전부터 기술연구소를 통해 자동차용 강종의 선행연구를 시작해 지난 2014년까지 5년간 총 87종의 자동차용 강판을 개발했으며 실제 완성차 적용을 점차 늘려가고 있다.
◇ 완성車 강판 수요 ‘완벽 대응’ 체제 갖춰
현대제철은 고로 가동 첫 해인 2010년에 내판재와 섀시용 강판의 강종 전부인 49종을 개발한 것을 시작으로 2011년에는 외판재 12종과 고강도강 등 22종을 개발했다.
지난 2012년에는 100~120K급 초고장력강 등 10종을 개발, 현재 자동차에 사용하고 있는 전 강종(81종)을 개발 완료해 완성차의 강판 수요에 완벽히 대응할 수 있는 체제를 갖췄다.
2013년 이후에는 고성능ㆍ고강도의 자동차용 신강종 개발에 주력해 고강도 열연도금강판 등 6종의 강종 개발을 추가 완료하며 2014년까지 총 87종에 대한 양산체제를 구축했다. 올해 들어서도 지난 상반기까지 구조보강용 150K급 초고강도 냉연강판과 180K급 핫스탬핑강 선행개발을 완료하는 등 초고강도강(AHSS) 개발이 꾸준히 이뤄지고 있다.
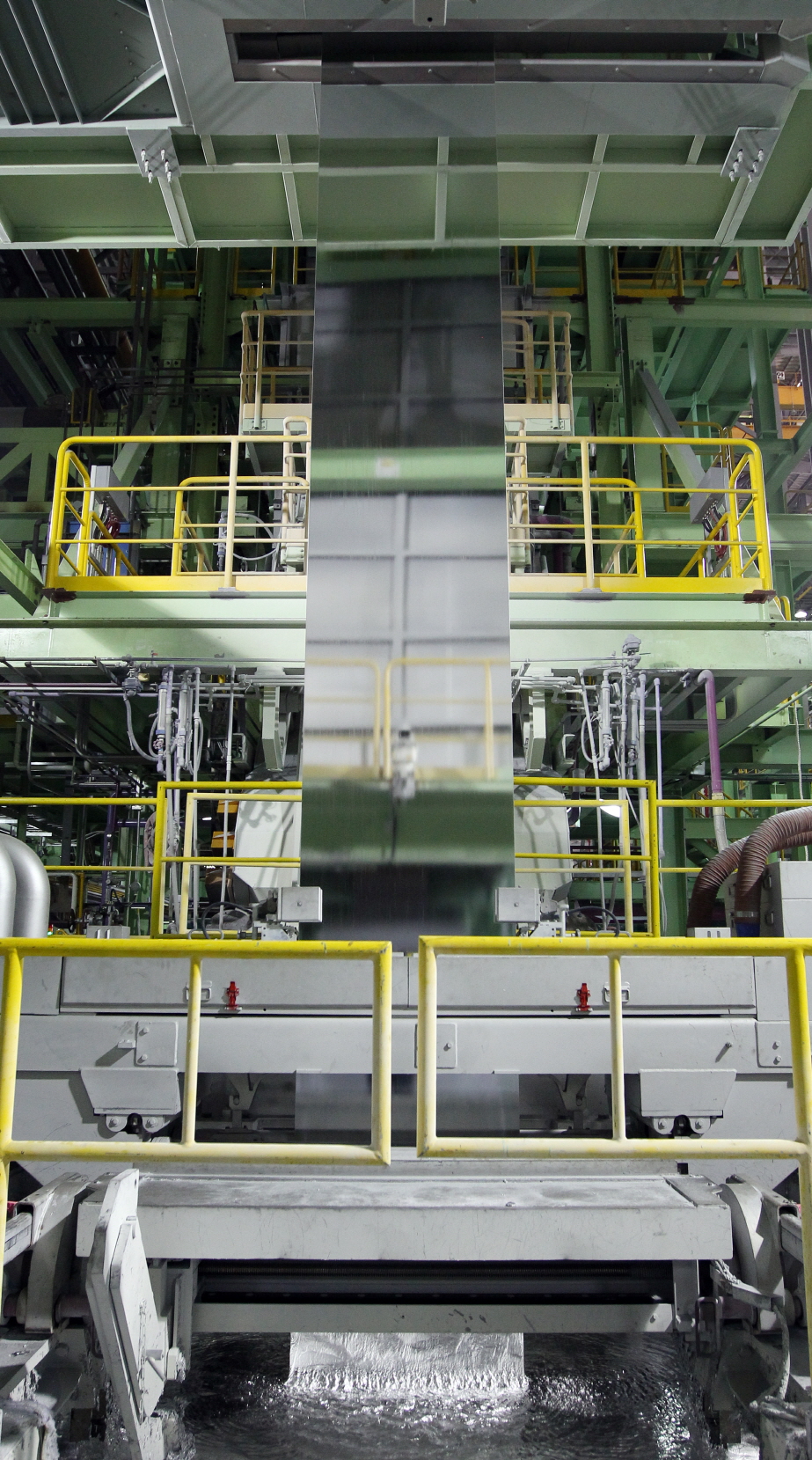
자동차산업협회에 따르면, 올해 전 세계 자동차 생산은 9,300만대(판매 전망은 8,750만대) 전후를 기록하고 오는 연평균 3.5% 성장하면서 2020년에 1억대 생산을 돌파할 것으로 예상되고 있다. 이에 따라 자동차강판 수요는 연평균 2.6% 증가가 예상된다. 이 가운데 AHSS 증가율은 연평균 15.5%로 높은 성장세를 이어갈 전망이다. 이러한 수요 증가 전망 속에 현대제철의 발빠른 AHSS 개발은 자동차 및 철강업계의 이목을 끌고 있다.
<표>현대제철 자동차 강판 개발 현황
: 2012년 자동차용 전 강종(81종) 개발 완료. 2014년 자동차용 87종 양산체제 구축
구 분 |
2010년 |
2011년 |
2012년 |
2013년 이후 |
개발방향 |
내판재 |
외판재 전체 |
외판 신강종 |
열연도금강판, 고강도 신강종 개발 |
섀시 전부품 |
고강도강 |
초고강도강 |
||
개발강종 수 |
49종 |
22종 |
10종 |
6종 |
주요 개발강종 |
일반ㆍ고성형 내판재 : 대시판넬, 플로어 |
외판재 : 12강종 전체 |
외판 고강도 강판 |
열연도금강판 |
도어 인너 등 |
루프 / 도어 / 펜더 |
50K급(도어) 내판 열연 고강도강 |
||
후드 / 사이드아우터 |
80K급 (섀시) |
|||
고강도강 60K급 |
고강도강 60~80K급(590DP, 780DP) |
초고강도강 100~120K급 |
|
현재 세계 자동차산업은 연비 및 배출가스 규제 강화로 차량 경량화 요구가 커지면서 초고장력강 사용을 늘리면서 경량화에 대응하는 수준이 높아지고 있다. 특히 차량경향화는 소비자 실사용 조건에서 연비 개선에 보다 직접적인 영향을 주고 있기 때문에 차량경량화 요구는 연비 규제 대응을 위한 필수불가결한 기술요소로 꼽힌다. 자동차 업계에서는 차량경량화 10%를 통해 연비가 4% 개선된다고 분석하고 있다. 이에 따라 현대제철은 자동차 충돌성능 및 경량화 요구에 부응하기 위해 초고장력강판 개발에 집중해 왔다.
신차 기준으로 2013년 12월 출시된 신형 제네시스(제네시스DH)에 냉간 성형용 초고장력 강판이 본격적으로 확대 적용되기 시작했으며, 외판 및 차체구조용을 비롯, 고강도 충돌 구조 부품용으로 핫스탬핑 강판 등 80K~150K급 강판을 양산하는 등 초고강도 강판 공급 확대에 주력하고 있다. 지난 3월 출시된 ‘2015 제네시스’에는 60K 이상 초고장력강이 51.5% 적용됐는데 강도실험 결과 BMW 5시리즈보다 1.6배 강한 것으로 나타났다. 초고장력강 중에서도 150K급은 11.8%, 100∼120K급 8.6%, 60∼80K급이 31.6%이 각각 적용됐다.
제네시스 외에도 LF소나타, 아슬란, 투싼, K5, 스포티지 등 새롭게 출시되는 현대ㆍ기아차의 신차종의 가장 큰 특징 중 하나는 초고장력강 적용이 크게 증가했다는 점이다.
통상적으로 양산차에 적용하기 위해서는 랩 테스트(LAB Test)와 필드 테스트(Field Test) 등에 최소 2년 이상의 시간이 필요하다는 점을 감안하면 현대제철이 개발한 신강종들은 향후 현대ㆍ기아차 신차에 속속 적용될 것으로 예상된다.
현대차그룹은 신차 차종 투입이 확대되는 2016년 이후로도 글로벌 판매를 확대해 2018년에는 연간 1,000만대 이상 판매를 계획하고 있다. 이를 위해서는 가장 핵심적인 자동차용 강판의 안정적인 공급과 고품질화가 필수적이기 때문에 현대제철의 역할은 더욱 중요해질 전망이다.
<표>현대ㆍ기아차 초고장력 강판 적용 비율
기존 |
신차 적용 (’14년 이후) |
||
준중형 SUV |
|
준중형 SUV |
|
(투싼) |
18% |
(2016 투싼) |
51% |
(스포티지) |
18% |
(2016스포티지) |
51% |
중형 세단 |
21% |
중형 세단 |
51% |
(쏘나타 YF) |
(쏘나타 LF) |
(핫스탬핑강 12%, 80~120K급 16%) |
|
대형 |
14% |
대형 |
51% |
(제네시스BH) |
(제네시스 DH) |
(핫스탬핑강 11%, 80~120K급 17%) |
◇ 차세대 자동차용 독자 신강종 개발 박차
현대제철이 자동차강판 개발에 본격 뛰어든 것은 한보철강 인수 후 기술연구소를 설립한 2006년 무렵부터다. 그 뒤 당진에 첫 고로가 완공된 2010년부터 자체 생산한 열연강판으로 자동차강판 제조를 시작했다. 고로 건립과 동시에 자동차강판을 생산해낸 것은 세계적으로도 드문 사례다. 일관제철소 가동 이전부터 선행연구를 통해 기본 강종 개발에 집중했기 때문이다. 현대제철은 지난 2013년부터 자동차강판 중장기 강종개발 방향을 ‘신강종ㆍ미래강종 개발을 통한 경쟁력 강화’에 초점을 맞추고 현대제철만의 차세대 자동차용 신강종 개발에 주력하고 있다.
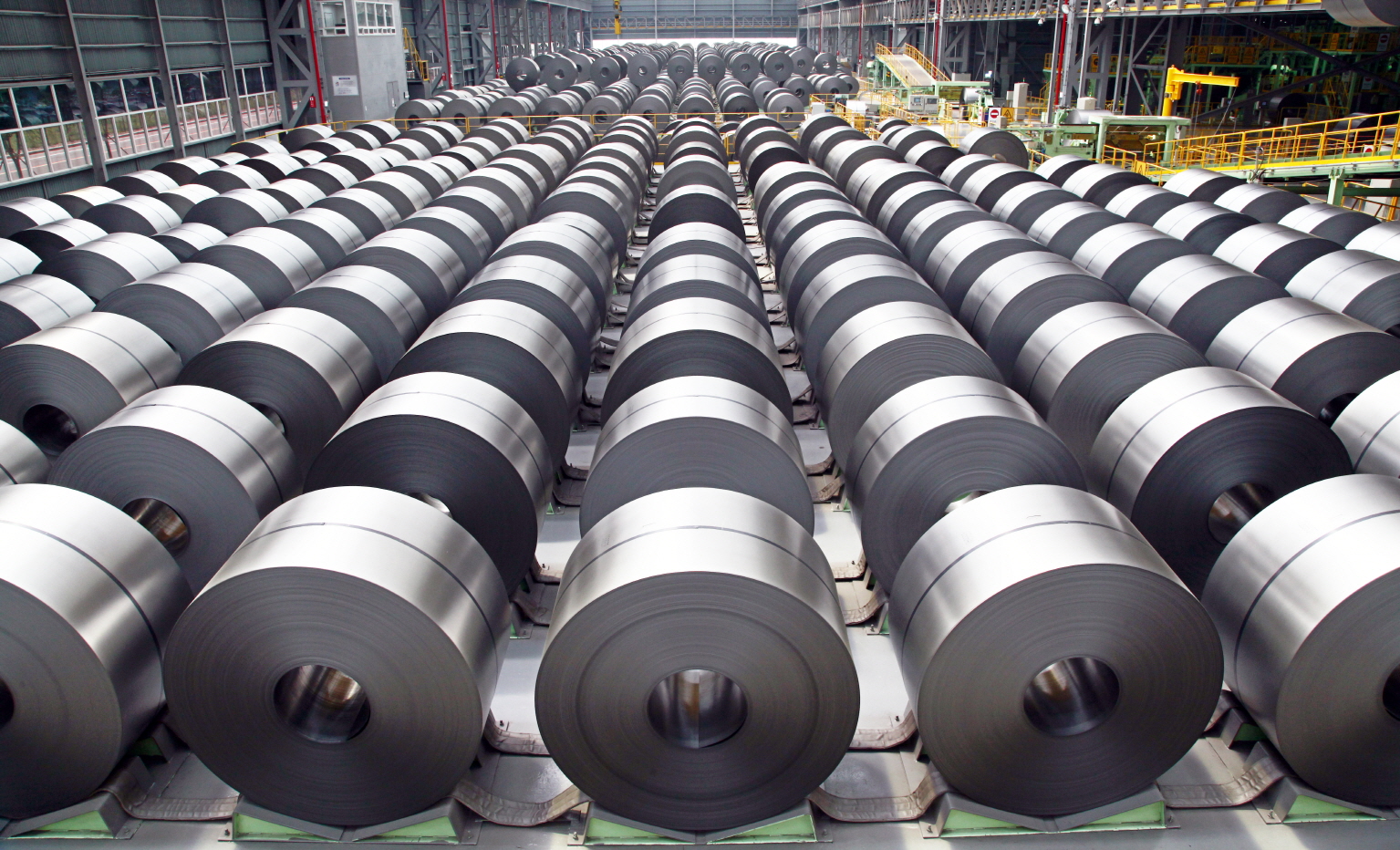
초고장력 양산체제를 갖춘 2013년에는 현대제철 고유의 자동차 섀시용 고강도 열연 산세강판(PO) 및 고강도 열연도금재(HGI)를 개발해 자동차의 성능과 안전에 중요한 역할을 하는 섀시 부품의 고강도화 및 방청성 향상을 이뤘다. 또한 강종 개발이 가장 까다로운 분야로 평가받고 있는 자동차용 외판재 역시 고강도를 유지하면서도 가공 성형성을 한층 높인 고성형성 초고강도 외판재를 개발하는 등 독자 신강종 개발에 성공했다.
이에 따라 현대제철 역시 부품별 특성에 맞게 설계된 고유의 특화강종 개발 및 적용을 진행하고 있다. 외판용의 경우, 고성형 외판 개발 및 성형기술 개발을 진행 중이다. 개발 막바지단계인 AMP(다상복합조직강)가 대표적이다. AMP는 강도 100K 이상, 연신율 20~30%의 성능을 갖는 강종으로 알려졌는데 내년초 시생산이 가능할 전망이다. 내년에는 초고강도 차체구조용강, 샌드위치강판, 고망간강, 저비중 경량강판 등의 개발을 완료할 것으로 보인다.
구조보강용 부품은 강도를 개선하면서도 연신율이나 굽힘 가공성이 향상된 고강도, 고성형 초고장력강 개발이 병행되고 있다. 마찬가지로 이를 부품에 적극 적용할 수 있는 성형 및 해석, 용접, 도장, 방청기술 개발 역시 진행하고 있다. 특히 TWB, 핫스탬핑, 열간성형가공 기술 등에 주력하고 있다.
앞으로 현대제철은 강도는 물론 성형성을 획기적으로 개선한 3세대 강판 개발뿐만 아니라, 고굽힘성 강판, 고인성 강판, 고버링성 강판 등 자동차 부품별 특성에 최적화된 맞춤형 강판 개발에 주력할 방침이다.
또한 기존 초고강도 소재와 신기술을 융합해 경량화, 고강도화한 TWB 핫스탬핑, 통전가열 성형기술 등 다양한 연구를 통해 경량 차체에 대한 철강재의 경쟁력을 높임으로써 미래자동차의 요구에 발 빠르게 대응해 나갈 것이다.
이렇듯 전 세계 어느 철강사보다 빠르게 다양한 자동차강판 생산체제를 구축한 데에는 기술연구소의 역할이 크게 한 몫 하고 있다. 지난 2007년 당진제철소 내에 개설한 기술 연구소를 통해 재료분석에서부터 열연 및 냉연공정 모사실험 등 철강 소재 관련 연구는 물론 자동차 강판의 성형 및 가공기술을 개발하고 이를 유통 및 가공업체에 제공함으로써 부품업체들과의 동반성장에도 적극적으로 나서고 있다. 현대차와 현대제철, 그 협력사까지 힘을 합친 공동연구를 통해 세계에서 유래를 찾아볼 수 없을 정도로 빠르게 자동차강판 품질을 확보할 수 있게 됐다.
현대제철은 다른 철강업체들이 하기 어려운 현대ㆍ기아차와의 적극적인 협업을 바탕으로 자동차 강판은 물론 다른 소재에 대한 응용기술 개발에도 적극적으로 나설 수 있다는 장점을 갖고 있다. 현대ㆍ기아차가 글로벌 1,000만대 생산체제를 구축하기 위해 노력하고 있는 만큼 현대제철의 자동차 강판 기술력 확보와 물량 확대는 꾸준히 이어질 것으로 예상된다.
여기에 해외 SSC를 확보함으로써 자동차 강판의 기술 및 품질 관리능력을 강화해 해외 자동차 강판 수요 변화에 적극적으로 대응할 수 있는 준비를 마쳤다. 아직까지 그룹사 공급에 전력투구하고 있어서 타 자동차사의 요구에 대응하기가 쉽지 않지만 앞으로 고부가가치 제품 개발과 선제적 강종 개발 등을 통해 글로벌 경쟁력을 갖출 가능성도 매우 높아 보인다.
[현대제철의 자동차강판 주요 강종 개발 및 적용 현황]
△ 방청 수명 향상 위한 초고강도 열연도금강판(PO) 개발
- 크로스멤버, 로어암 등 섀시 부품의 강도와 방청성능을 강화한 초고강도 열연도금강판 개발 완료. 2014년 LF쏘나타부터 적용
- 크로스멤버: 차체의 언더 보디 등에 쓰이는 뼈 모양의 부품으로 앞뒤 좌우 방향의 뒤틀림과 구부러짐을 막기 위해 사용됨
- 로어암: 자동차 본체와 바퀴를 연결하는 서스펜션 암의 종류 중 하나
- 사이드아우터: 차체 측면의 외판재로 높은 성형성을 요구하는 강판
△ 50K급 외판을 도어 뿐 아니라 후드 및 펜더까지 적용
- 성형성 한계로 기존에 35K급 강판을 사용하던 도어, 후드, 펜더에 성형성을 확보한 50K급 외판 개발
- 2012년 싼타페DM 차종 이후 신차에 적용되고 있음
△ 32K급 사이드 아우터용 고강도 강판 개발
- 사이드아우터 등 자동차 외판재는 강도보다는 미려함, 성형성이 중요하여 강도가 낮은 강판을 사용
- 특히, 사이드아우터용 강판은 외판 중 가장 높은 성형성이 요구되어 28K급이 널리 사용되고 있음
- 상대적으로 고강도인 32K급 강판의 성형성 한계를 개선해 2015년 세계 최초로 개발 완료
△ 고성형 초고장력 냉연강판
- 충동부재 경량화 및 충돌성능 향상 위한 초고장력강 확대 적용 필요
- 초고강도 및 고성형 동시 확보 가능한 고성형 120~150K급 냉연강판 개발 중